Industrial flooring demands durability, safety, and reliability. As a leading FRP grating supplier and manufacturer, we understand the critical role that quality grating solutions play across diverse sectors. This comprehensive guide explores how fiberglass reinforced plastic (FRP) grating is transforming industrial flooring applications.
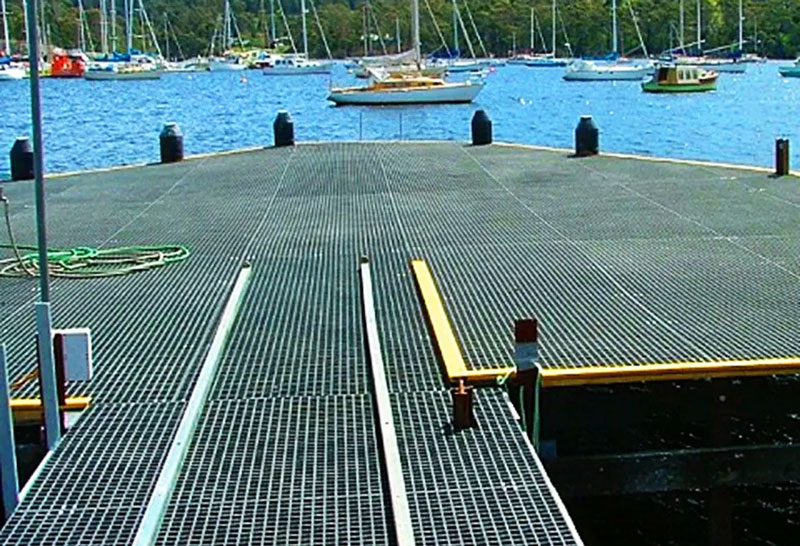
What Makes FRP Grating Superior to Traditional Materials?
The advantages of FRP grating over conventional materials are substantial. Its corrosion resistance and durability make it ideal for harsh environments like chemical processing facilities and marine applications. The lightweight nature of fiberglass grating reduces installation costs while maintaining impressive load-bearing capabilities.
Key benefits include:
- 75% lighter than steel alternatives
- Corrosion resistant in harsh environments
- Non-conductive properties
- Low maintenance requirements
- Extended service life
Understanding Molded vs. Pultruded Grating Systems
Molded and pultruded gratings serve different purposes based on application requirements:
Molded Grating:
- Manufactured through compression molding
- Excellent for high-traffic areas
- Superior impact resistance
- Ideal for heavy-duty industrial applications
Pultruded Grating:
- Continuous manufacturing process
- Higher strength-to-weight ratio
- Perfect for long spans
- Cost-effective for large installations
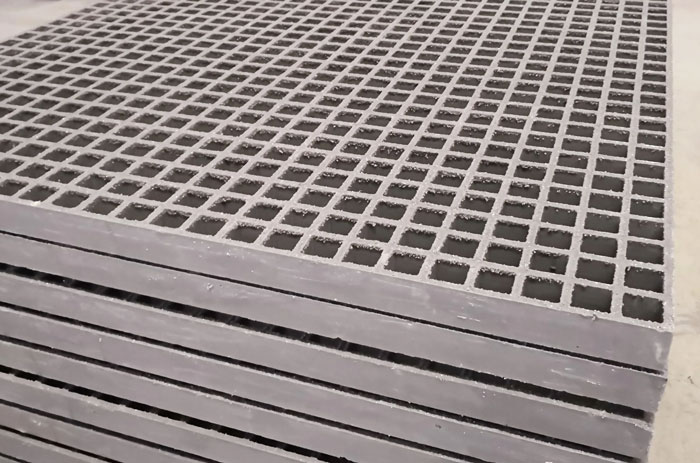
How Does Resin Selection Impact Performance?
The choice of resin system significantly affects grating performance:
Harztyp | Chemical Resistance | Heat Resistance | Cost Factor |
---|---|---|---|
Polyester | Good | Mäßig | ★★★ |
Vinylester | Exzellent | Hoch | ★★★★ |
Phenolisch | Superior | Very High | ★★★★★ |
Surface Options and Safety Considerations
Safety is paramount in industrial settings. Our temporary fence manufacturing expertise translates to superior grating solutions with various surface options:
- Grit-top surface for maximum slip resistance
- Plain top for general applications
- Custom surfaces for specific requirements
Size and Load Capacity Guidelines
Standard panel sizes typically range from:
- Width: 3′ to 4′
- Length: 8′ to 20′
- Depth: 1″ to 2″
Load capacity varies based on:
- Span requirements
- Support conditions
- Traffic patterns
- Environmental factors
What Industries Benefit Most from FRP Grating?
FRP grating proves invaluable across multiple sectors:
- Chemical Processing
- Offshore Platforms
- Water Treatment
- Food Processing
- Manufacturing Facilities
Installation and Maintenance Best Practices
Proper installation ensures optimal performance. Key considerations include:
- Proper support spacing
- Correct fastening methods
- Regular inspection schedules
- Cleaning procedures
Customization Options and Special Applications
Unser specialized manufacturing capabilities enable custom solutions:
- Color options
- Special sizes
- Custom patterns
- Application-specific designs
Environmental Benefits and Sustainability
FRP grating contributes to sustainable construction through:
- Long service life
- Reduced maintenance
- Lower carbon footprint
- Recyclability options
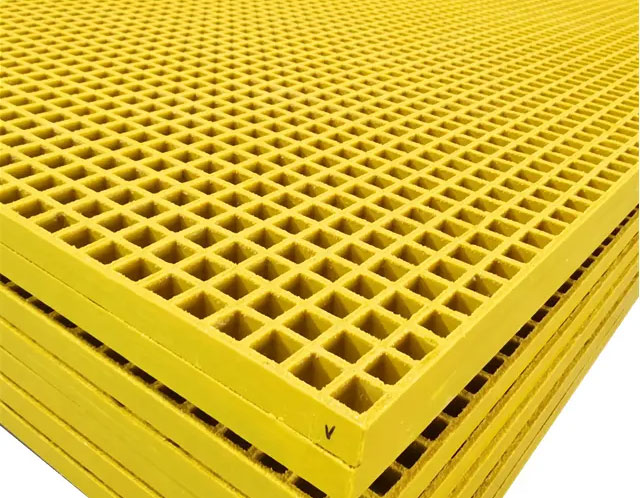
FAQs
How long does FRP grating typically last?
With proper maintenance, FRP grating can last 25+ years in normal conditions.
What is the maximum load capacity for standard FRP grating?
Standard panels can support up to 500 psf with proper support spacing.
Can FRP grating be cut on-site?
Yes, using appropriate tools and following safety guidelines.
Is special maintenance required for FRP grating?
Minimal maintenance is needed – typically just periodic cleaning and inspection.
Die wichtigsten Erkenntnisse
- FRP grating offers superior corrosion resistance and durability
- Multiple resin systems available for specific applications
- Customizable solutions for diverse industrial needs
- Cost-effective long-term flooring solution
- Environmentally sustainable choice
- Low maintenance requirements
Contact our expert team today to discuss your specific grating requirements and discover how our solutions can benefit your facility.